Unlocking Innovation with Prototype Injection Molding
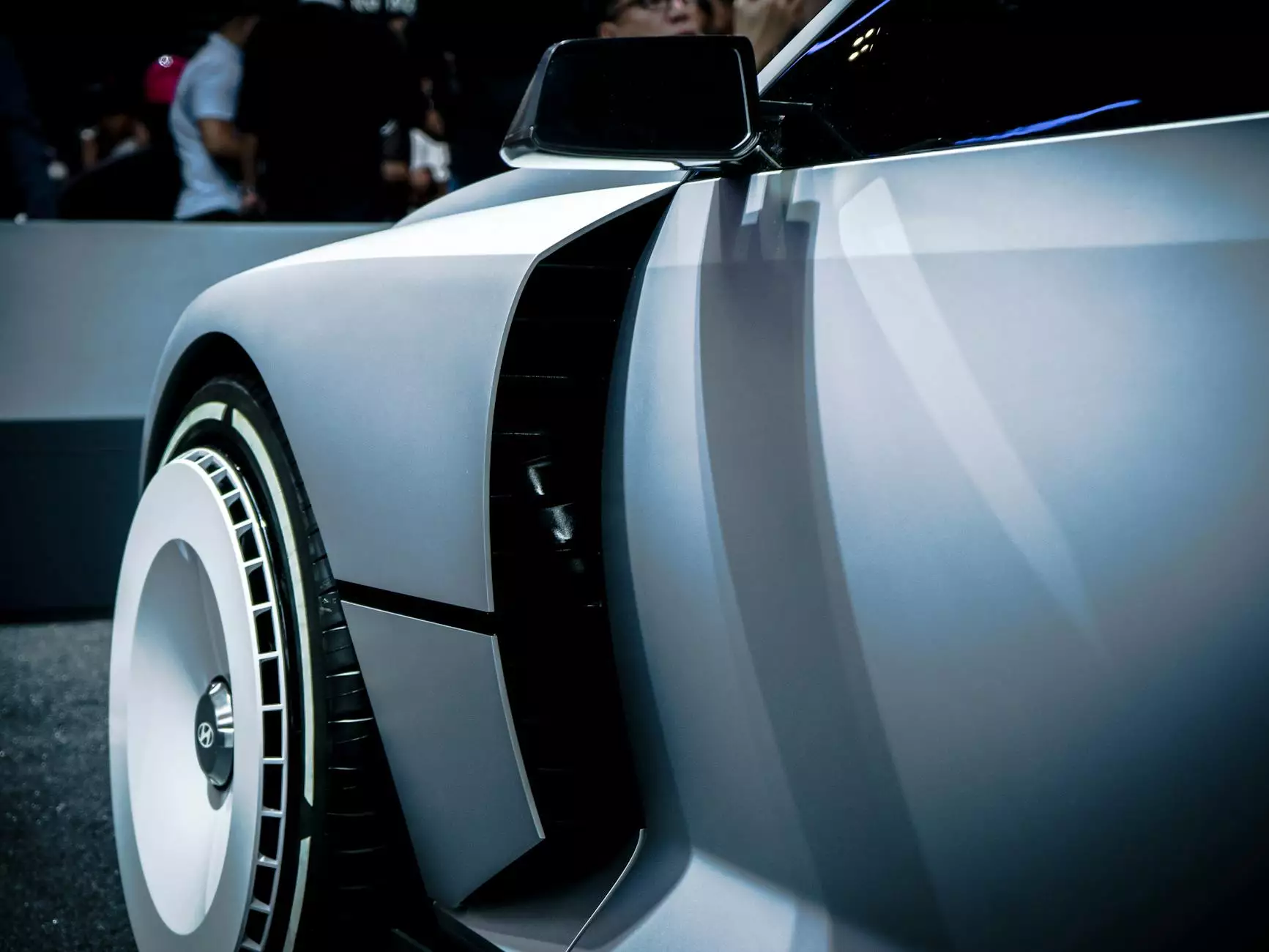
In today's fast-paced business landscape, prototype injection molding stands as a cornerstone for companies seeking to innovate while minimizing costs. This advanced manufacturing process allows for the rapid development of prototypes, enabling businesses to test designs and concepts before full-scale production. In this comprehensive guide, we will explore the intricacies of prototype injection molding, its advantages, applications, and why it is critical for industries, particularly for companies in the metal fabrication sector.
What is Prototype Injection Molding?
Prototype injection molding is a specialized manufacturing process used to create parts and components by injecting molten material into a mold. This technique is particularly useful for producing complex shapes and intricate designs. The molds are typically made from steel or aluminum and are designed to be durable enough to withstand multiple cycles of production.
The Process of Prototype Injection Molding
The process of prototype injection molding can be broken down into several critical steps:
- Designing the Prototype: The first step involves creating a detailed design of the part or component, usually through CAD software. This stage focuses on functionality and manufacturability.
- Creating the Mold: Once the design is finalized, a mold is fabricated. Depending on the complexity, this can involve CNC machining or 3D printing.
- Injection Molding: The selected material, often thermoplastic, is heated until it becomes molten and is then injected into the mold under high pressure.
- Cooling and Ejection: After the molten material fills the mold, it cools and solidifies. The mold is then opened, and the finished part is ejected.
- Finishing Touches: The prototype may undergo additional processes such as trimming, polishing, or surface treatment to enhance its appearance and functionality.
Benefits of Prototype Injection Molding
Utilizing prototype injection molding offers several distinct advantages for businesses:
- Cost-Effectiveness: By creating prototypes quickly and efficiently, companies can save significant costs associated with material waste and labor.
- Speed to Market: Rapid prototyping allows businesses to test and modify designs swiftly, facilitating quicker market entry.
- Precision and Quality: Injection molding produces highly accurate parts, ensuring consistency and quality in the final product.
- Reduced Risk: Prototyping enables businesses to identify design flaws early in the development process, significantly reducing the risk of costly errors during full production.
- Material Variety: A wide array of materials can be used in injection molding, allowing for flexibility in design and function.
Key Applications of Prototype Injection Molding
Prototype injection molding is applicable across various industries, but its utility is especially pronounced in the following sectors:
1. Automotive Industry
Within the automotive sector, prototype injection molding is pivotal for developing components such as dashboard assemblies, lighting components, and gear knops. The need for rapid testing and design adjustments makes it invaluable to automotive manufacturers.
2. Consumer Electronics
For companies in consumer electronics, producing parts like housings and aesthetic covers quickly allows for product iterations and innovations without extensive re-tooling costs.
3. Medical Devices
The medical industry benefits from prototype injection molding due to the necessity for compliance with stringent regulations. Rapid prototyping allows for the development of devices such as syringes and surgical instruments with precision and, importantly, the ability to iterate designs for improved safety and efficacy.
4. Industrial Equipment
Manufacturers in industrial sectors often utilize prototypes for components like machine parts and casings, where reliability and durability are essential. Injection molding allows for testing the components' performance under actual working conditions.
Choosing the Right Partner for Prototype Injection Molding
When selecting a partner for your prototype injection molding needs, consider the following factors:
- Expertise and Experience: Look for manufacturers with a proven track record in your industry.
- Quality Assurance: Ensure they have stringent quality control processes in place to meet industry standards.
- Technological Capabilities: Choose a partner who invests in the latest technologies and materials for optimized production.
- Customer Support: A collaborative approach to prototyping is essential. Your partner should provide excellent customer service and be willing to accommodate design changes as needed.
The Future of Prototype Injection Molding
As technology advances, the future of prototype injection molding looks promising. Innovations such as advancements in 3D printing and automation are significantly enhancing the production capabilities and possibilities. Furthermore, the trend towards sustainable materials signifies a shift that will impact how products are designed and manufactured in the years to come. As industries increasingly adopt these technologies, the efficiency and effectiveness of prototype injection molding will only continue to grow.
Conclusion
Prototype injection molding is an essential process for modern businesses looking to innovate while optimizing time and costs. By understanding its benefits, applications, and the intricacies of the manufacturing process, companies can leverage this powerful tool to stay ahead of the competition. Whether you are in the automotive industry, consumer electronics, medical devices, or industrial equipment, the ability to create precise, high-quality prototypes can significantly enhance your product development cycle.
For businesses in the metal fabricators domain, tapping into the advantages of prototype injection molding can lead to improved product offerings and enhanced market competitiveness. Remember to choose a capable and experienced partner that aligns with your manufacturing needs to maximize the benefits of this innovative approach.
As you embark on this journey of innovation, embracing the capabilities of prototype injection molding can set the stage for a successful future in your industry.